For nearly four decades, Shotton Paper Mill in Wales was a paper production facility, its machinery humming as it churned out massive rolls of material for newspapers and packaging. But times change, and with sustainability becoming a driving force in the industry, the mill faced a new challenge – reinventing itself for the future.
The decision was made to convert the facility into a cutting-edge cardboard production plant, a shift that required not just new machinery, but a complete structural overhaul. The facility needed to accommodate new production lines, integrate modern sustainability measures, and ensure that every component – from steel frameworks to in-situ concrete – worked together seamlessly. To achieve this, the project team at ENKA turned to an innovative composite structural system, blending steel and precast elements in a way never before seen in a paper mill.
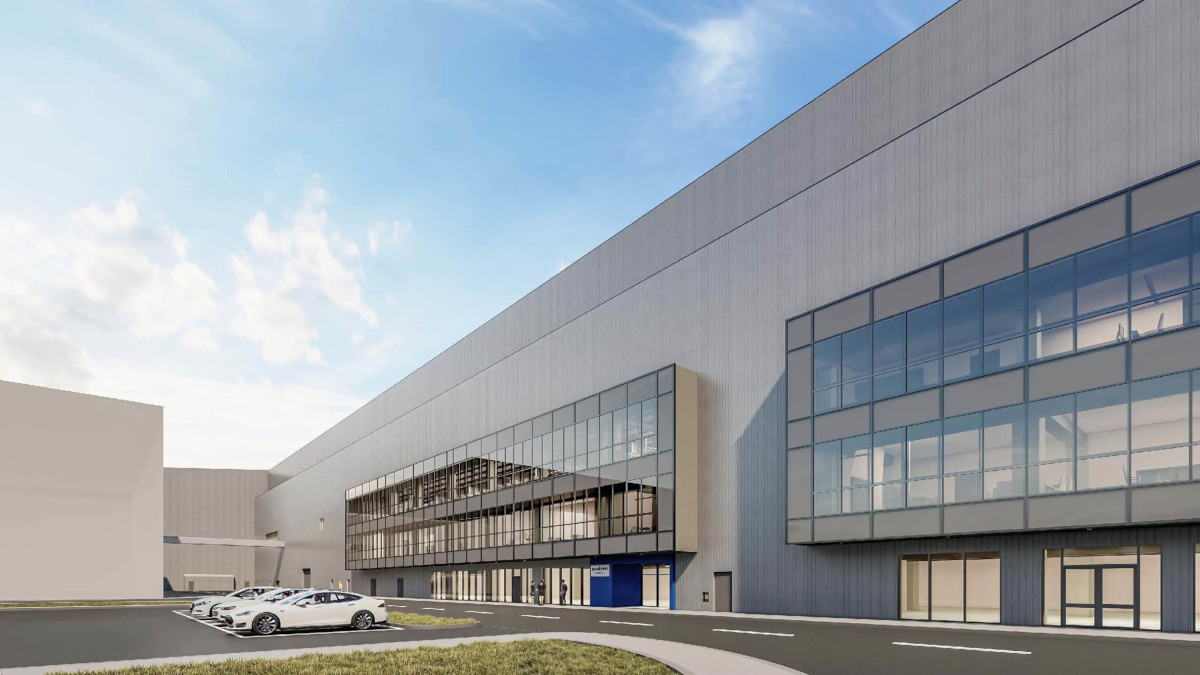
Building a New Foundation
At the heart of this transformation was the new structural system. Unlike traditional mill structures, which often rely on either steel or concrete as primary load-bearing elements, this design combined precast concrete components for durability and stability with steel members for flexibility and strength. This hybrid approach was particularly well-suited to an industrial facility undergoing a major conversion, as it allowed for greater adaptability in accommodating new machinery and production layouts while ensuring the structural integrity of the building.
One of the key benefits of this system was its ability to support heavier loads and wider spans without requiring extensive on-site concrete pours, which could slow down construction. The precast elements were manufactured off-site and then assembled on location, reducing overall build time and ensuring consistency in quality. Meanwhile, the steel framework allowed for more efficient connections between structural components, providing the strength needed to support high-performance manufacturing equipment.
However, introducing this composite system also presented challenges. Firstly, the redevelopment wasn’t just about a single structure – it involved an interconnected network of facilities, including the Paper Mill Building, Effluent Treatment Plant (ETP), Water Treatment Building (WTP), Starch Building, and a dedicated power plant (CHP). Each played a critical role in ensuring the facility could operate efficiently in its new capacity.
Coordinating the integration of steel and precast elements of all these structures required careful planning, particularly where load transfers and connections between materials occurred. Every joint, support, and load-bearing structure had to be carefully modeled and tested to ensure that the two materials worked together seamlessly.
With so many moving parts, precision was key. However, this wasn’t just a structural challenge – inside the mill, specialized machinery and infrastructure also had to be accommodated, adding another layer of complexity to the design. The risk of clashes between any of these critical elements could lead to costly delays or inefficiencies in the production process. To avoid this, the design team relied heavily on 3D modeling and digital workflows to refine the integration process before construction even began. “Using the 3D model helped us to identify where there were clashes between the structural members, as well as integrate the in-situ structural members with the new precast and steel members,” explains Murat Sungur, Civil Design Coordinator at ENKA.
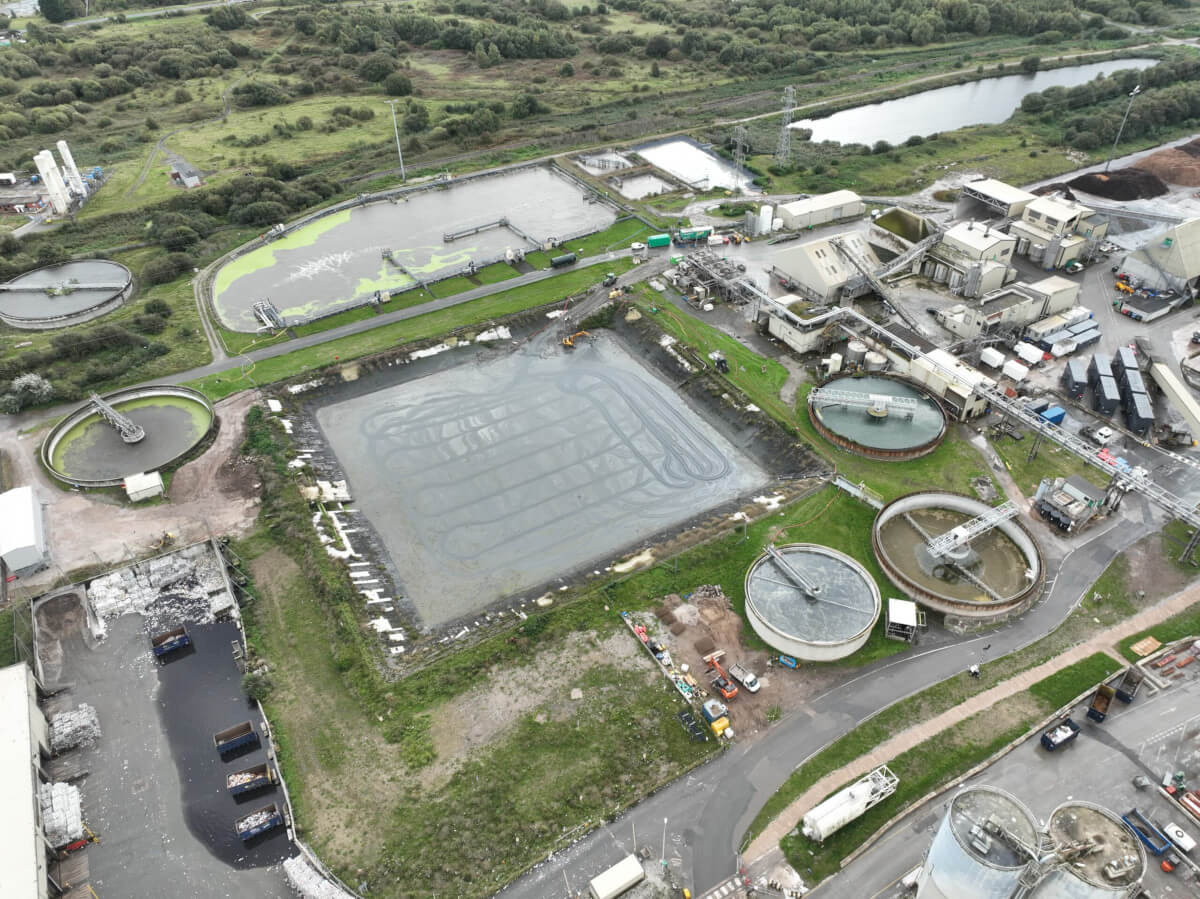
Solving the Puzzle with 3D Modeling
Managing a project of this scale was no small feat. With multiple companies involved in the design process, ensuring everyone worked from the most up-to-date plans was one of the biggest challenges. As designs evolved, keeping structural, mechanical, and architectural elements aligned required careful coordination. Any miscommunication or outdated information could lead to costly delays, rework, or even structural conflicts.
Beyond coordination, the integration of steel, precast, and in-situ concrete presented additional complexities. Each material had unique load-bearing properties and connection requirements, meaning every joint and transition point had to be precisely planned. The composite nature of the structure meant that precast members had to be placed in exact locations to support steel elements, and any misalignment could create cascading issues throughout the build.
To tackle these challenges, the project team relied on advanced 3D modeling with ALLPLAN 2024 to ensure precision at every stage. By creating a detailed digital representation of the mill, they could visualize how each structural element interacted, identify clashes before they occurred, and streamline decision-making. This was particularly crucial in areas where structural elements had to work in harmony with heavy machinery and production infrastructure – ensuring that nothing interfered with operational efficiency once the facility became fully operational.
Additionally, the use of ALLPLAN’s 3D modeling facilitated smoother collaboration between disciplines, particularly with MEP designers responsible for integrating utilities and services. The ability to overlay structural models with mechanical and electrical designs allowed teams to proactively resolve conflicts rather than reacting to them on-site, reducing wasted time and materials.
By leveraging digital workflows and a data-driven approach, the team improved their accuracy and efficiency. “Using ALLPLAN helped us reduce the overall man-hours spent on the project, as well as prevented us from making any mistakes, saving further revisions and troubleshooting,” said Murat. What could have been a logistical nightmare instead became a highly coordinated and streamlined process, ensuring that the transformation progressed as smoothly as possible.
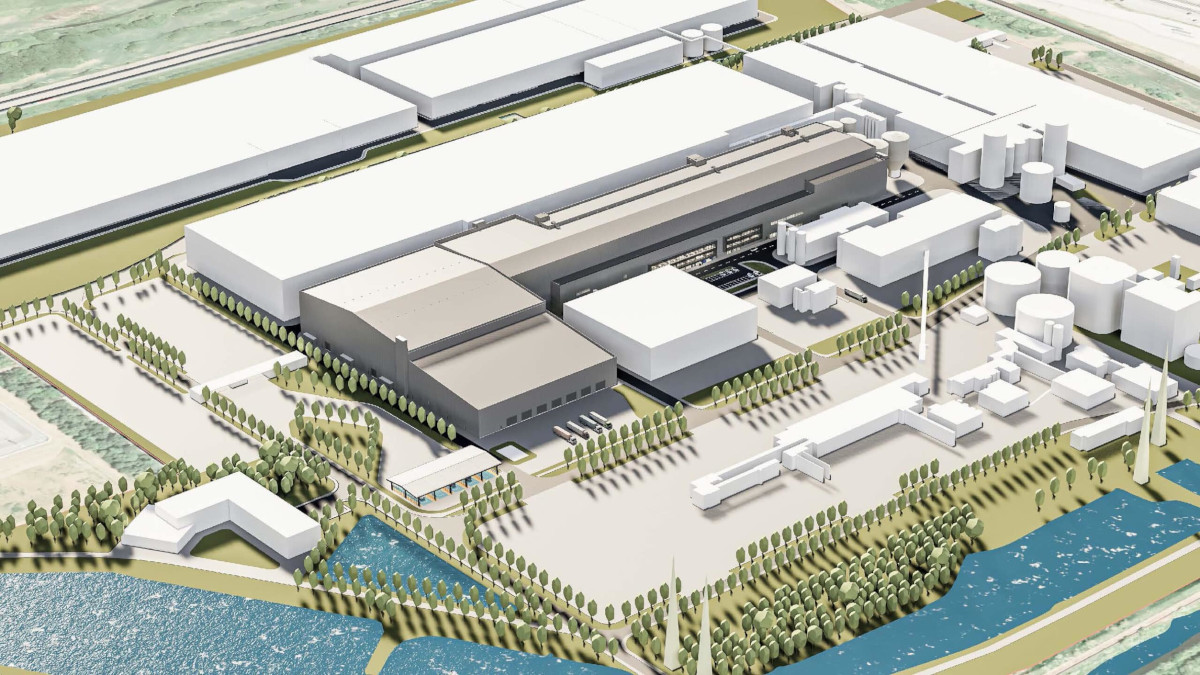
A Future Built on Innovation
The mill’s story isn’t just about a shift in production – it’s about transformation, innovation, and building for the future using digital workflows. What was once a traditional paper mill is now a forward-thinking facility designed for the future of sustainable packaging. And as sustainability continues to drive change, Shotton Paper Mill stands as proof that with the right tools, even the most established industries can evolve.
For the structural design team, this project is just the beginning. With the success of ALLPLAN in streamlining workflows and improving precision, there’s no question that digital tools will play an even bigger role in future developments. “As a structural design team, we know that 3D modeling and BIM is the future of design – and ALLPLAN is the right choice for this,” explains Murat. The lessons learned at Shotton will shape how they tackle new challenges, pushing the boundaries of what’s possible in industrial construction.