How automated workflows can save you time in precast design
Time is money: this has never been more true than it is today, especially in the construction industry. Cost pressure is also increasing enormously in the precast industry. The example of the Rütihof industrial park in Switzerland shows how automation can increase efficiency in precast projects.
The Swiss company METHABAU, acted as main contractor, taking over the project development, the complete design in 3D and BIM, the execution planning, as well as the construction services. Another project partner was Beton-Fertigteil-Union (BFU), who designs and produces precast concrete elements such as walls, slabs and structural precast elements in the Black Forest region of Baden-Württemberg, Germany. At Rütihof, BFU was responsible for the design, detailing, and production of the precast elements. From the very beginning, the two project partners relied on OPEN BIM to significantly reduce the coordination effort. Thanks to standardized workflows and templates, all parties involved gained more clarity. Any collisions and modeling errors were reliably detected when the specialist models were merged.

Automated workflows enable modeling in record time
In the Rütihof project, data exchange was optimized via IFC. METHABAU designed the building in 3D and BIM and then sent the data to BFU. With the help of the automated workflows in ALLPLAN Precast, BFU was able to quickly import the elements into ALLPLAN Precast and generate high-quality production plans and shop drawings. The IFC-Assistant and the MEP-Assistant were particularly helpful:
The IFC-Assistant converts imported IFC objects directly into intelligent precast elements. Self-drawn complex elements or imported 3D models are automatically converted into precast-specific component types and materials by means of attribute mapping.
The MEP-Assistant imports the MEP-model and synchronizes the imported fixtures with your catalogs. ALLPLAN quickly and easily converts non-standard IFC objects into customer-specific fixtures. Furthermore, the software detects and solves any clashes between the precast model and imported MEP objects.
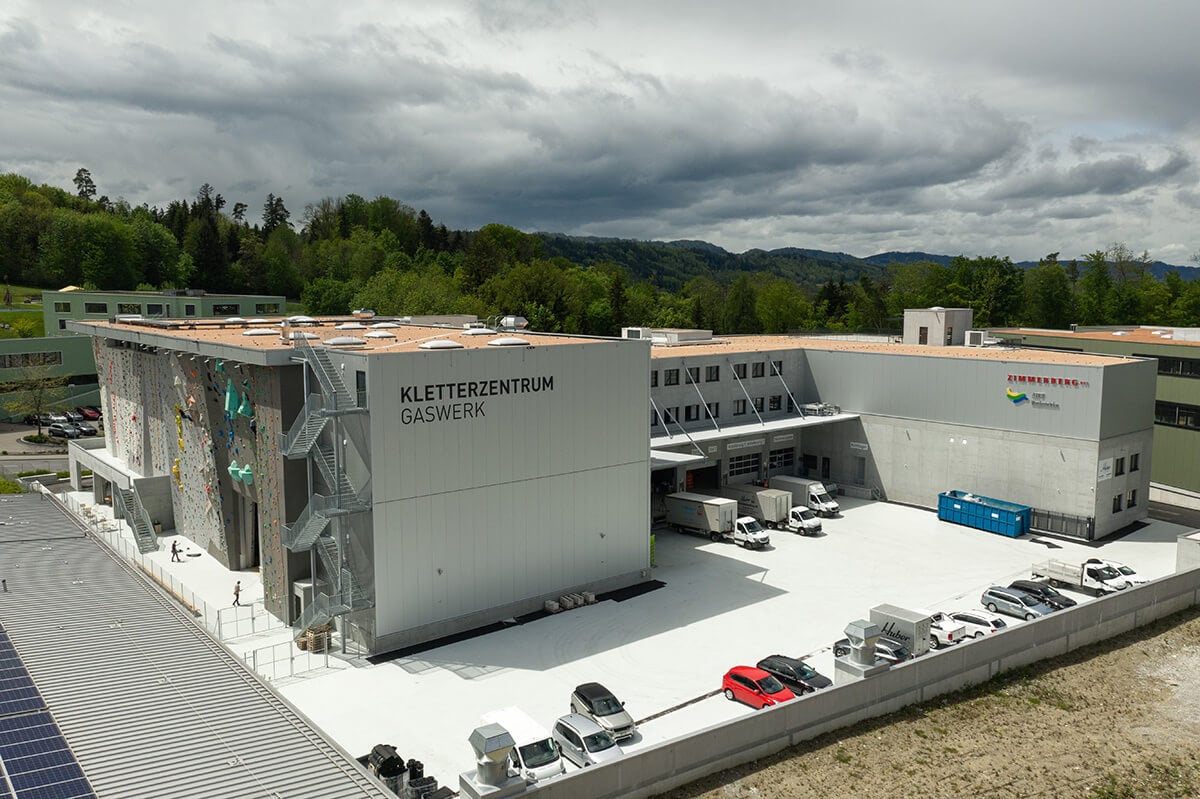
The efficiency gains provided by the automated shop drawing technology are one of the many reasons why BFU has long relied on ALLPLAN Precast. Within just nine months, BFU designed and produced an impressive 10,000 m² of slabs, 1,100 m² of solid walls, and around 40 stair elements. 360 truckloads brought the precast elements to the construction site in Wädenswil, Switzerland – all on schedule.
Three different tenants now occupy the 14,000 m² of usable space: There is an underground garage with 60 parking spaces for coaches, including a washroom with a column lift and a repair workshop. The beverage store has a multi-story logistics hall for the beverage trade, with an automatic pallet conveyor system over three floors and ten truck ramps. The Gaswerk AG climbing center is one of the largest indoor climbing centers in Europe and has facilities for all Olympic disciplines. The 18-meter-high climbing hall includes climbing routes with over 6,000 running meters, a bouldering room and, a 1,700 m² outdoor climbing wall.
Learn more about precast design and detailing in the project Rütihof here.