In the construction of the new Thermoplan plant in Weggis, those responsible have so far been very successful with combining BIM and integrated project management – a first in Switzerland.
Restaurateurs around the world associate the name Thermoplan with high-quality fully automatic coffee machines. As the increasing demand for the appliances is now (once again) exceeding production capacity, the company is currently building a new plant – now the fifth at the company site in Weggis, Switzerland. The construction project reflects the client's affinity for technology and striving for maximum efficiency: in addition to BIM-based planning, those responsible are relying on integrated project execution (IPA). In a nutshell, this means that everyone involved pulls together from the outset in transparent collaboration. In addition to a smooth process, Thermoplan aims to achieve further added value with the BIM method, such as a building that is as sustainable as possible (aiming for LEED Platinum certification).
The most unique combination of BIM and IPA to date
The project is called "unique". The name says it all, as the combination of BIM and IPA is unique in Switzerland. But first things first. The new plant is a nine-story complex – including a two-story underground car park – which will house integrated production areas and logistics facilities as well as office space once completed. At around 100,000 cubic meters, the building volume is roughly equivalent to that of 100 detached houses – quite a feat for a planned construction period of just two years. The opening is scheduled for March 2024.
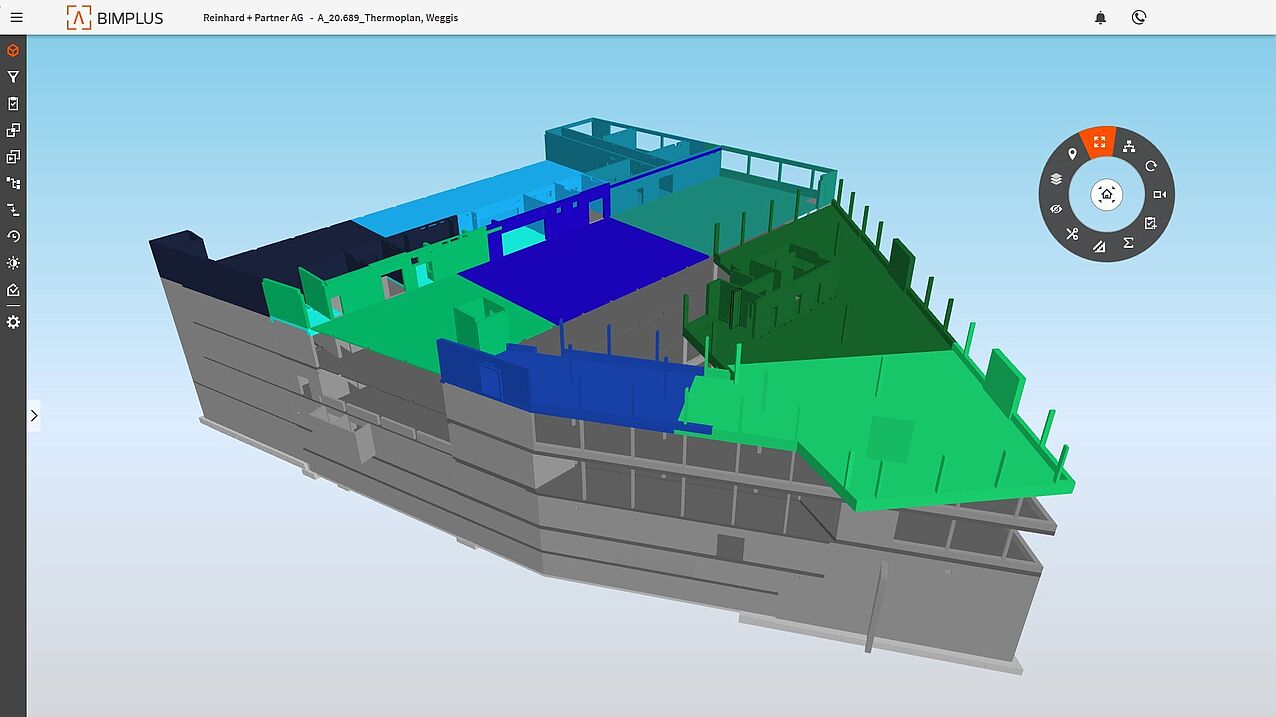
Paperless construction site thanks to BIM
The fact that the construction is so far on schedule is clearly thanks to the combination of BIM and IPA. All project participants were involved right from the start and were thus able to plan and organize the project together in stages. For example, Christen AG, which was entrusted with the execution of the project, started planning the construction process and the corresponding scheduling two years before the start of construction. For the construction company, unique is not only the first IPA project, but also its debut with a paperless construction site. For this purpose, there is a plan house with a large screen on the construction site, where all the necessary plans and information are available digitally.
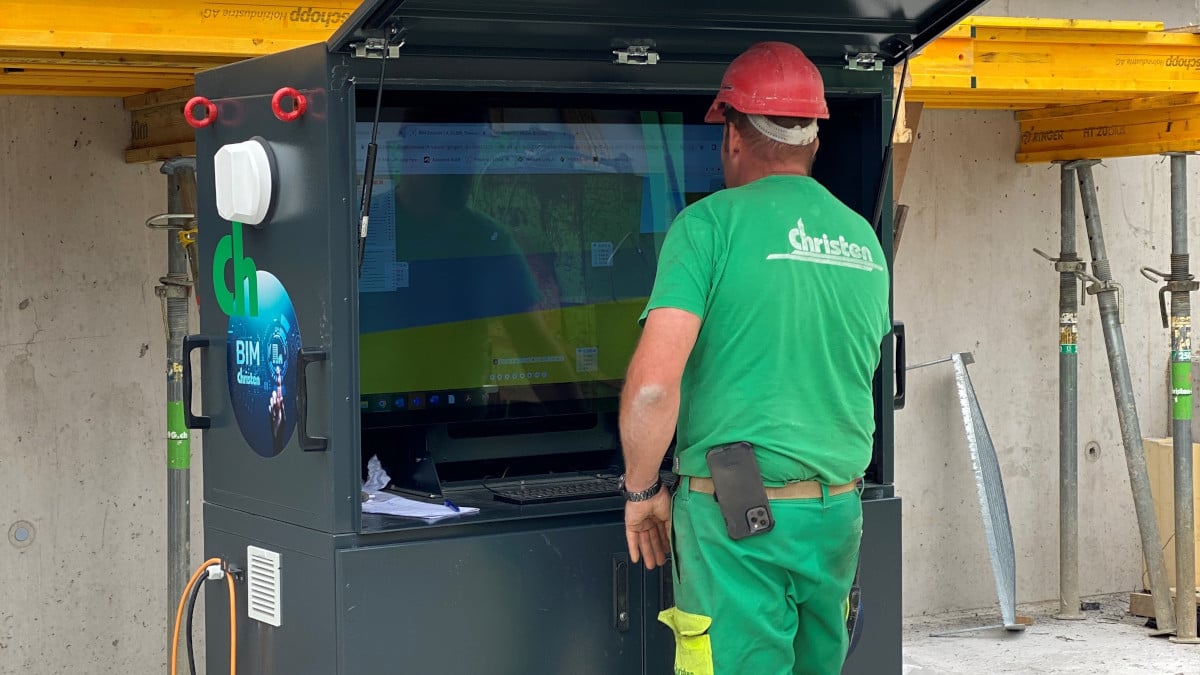
On-site access to models via Bimplus
The planning basis is a BIM model created by reinhard + partner AG in ALLPLAN, which the foreman can access on the construction site via Bimplus. In addition, the construction workers also had access to various specialist models such as an excavation model or individual formwork, reinforcement, and breakthrough models for each story via the BIM platform. Patrick Melli from ALLPLAN Switzerland, who usually also supports Christen AG as a BIM consultant, was responsible for coordinating and controlling the various models.
Christen AG impressed by BIM-based execution with Bimplus
Roman Christen, Head of Building Construction at Christen AG, is enthusiastic about the advantages of BIM-based execution with Bimplus and would not want to work any other way. For example, an IFC file can be generated from a component and simply loaded onto the measuring device without external help. Furthermore, dimensions can be derived directly from the model, and the ironworker can also easily obtain his information via Bimplus. Another major advantage would be the direct communication between foreman and engineer via the BIM platform, which would significantly reduce the workload of the foreman.
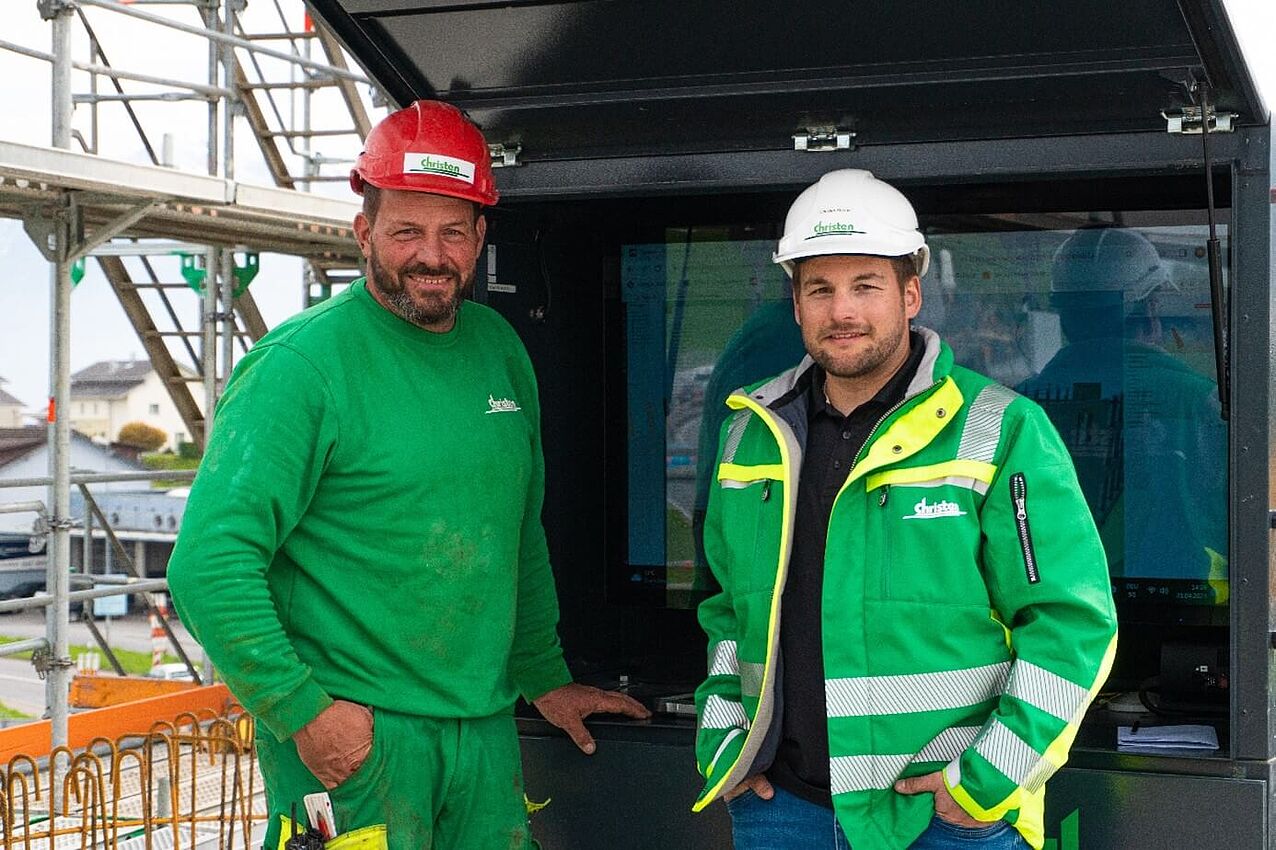
Eight crane cameras for Field2BIM
In the construction project, not only is digital data being implemented on the "BIM2Field" construction site, it is also being collected "Field2BIM". To do this, eight crane cameras capture 400 to 500 images a day, which together create an orthophoto of the construction site. This true-to-scale image can then be used to measure and document surfaces and cubatures as well as reinforcements and inserts.